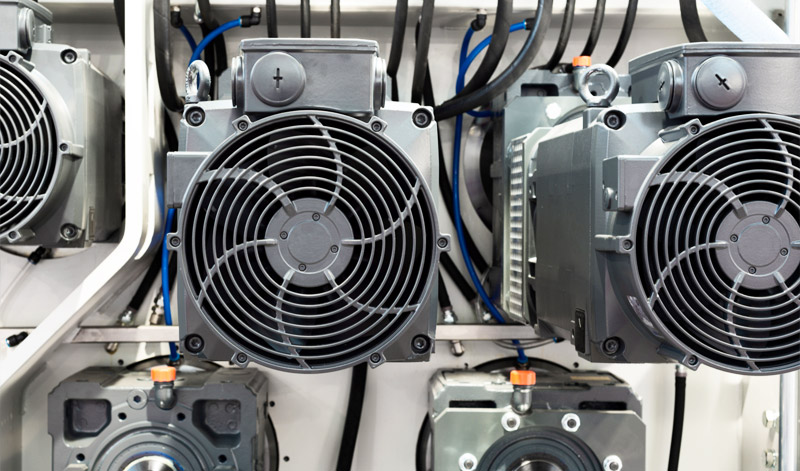
When Should Soft Start Devices be Applied to Motors?
When an induction motor starts, it often draws electric current that is much higher than the normal operating current—typically six to eight times higher. This peak inrush current can dim lights and trip breakers, causing delays and possibly affecting productivity.
Reduced-voltage starters and variable frequency drives (VFDs) can be used to decrease inrush current, which helps to eliminate power disturbances and extends equipment life by lessening mechanical stress. Each method, however, has advantages and disadvantages.
Reduced-voltage starters
Reduced-voltage starters are commonly used as a means of reducing the starting current of induction motors, but as the start current is reduced, the start torque is reduced by the current reduction squared. The current can therefore only be reduced to a level where the motor is still able to develop enough torque to start the driven load.
Commonly used reduced-voltage starters include auto transformer, primary resistance and solid-state soft starters. Solid-state soft starters utilize solid-state electronics to match voltage and current to provide the needed torque to start the motor. Because of their use of electronics, they provide greater accuracy and are better suited for use on systems with larger motors.
The main advantage of the solid-state soft start systems is more precise matching of the voltage and current, which reduces energy costs and stress on system components such as wiring, windings, fault protection equipment and breakers. However, soft start devices are typically used to control inrush current rather than to save energy. A drawback of solid-state systems is they cost more than conventional reduced-voltage starters.
Variable frequency drives (VFD) adjust the shaft speed of motors and allow for speed changes, increasing motor efficiency at lower speeds and reducing energy costs. VFDs work by converting alternating current (AC) to direct current (DC), and then converting the DC back to AC at a frequency that will drive the motor at the lower speed. In addition to speed control, VFDs provide built-in soft starting.
A major advantage of VFDs is they allow motors to start with an inrush current only slightly higher than the operating current. In comparison, a reduced-voltage starter has a typical inrush current of two to three times the full load current.
Despite their potential benefits, VFDs cost significantly more than reduced-voltage starters and they may not be a good fit for every application. It is important to carefully evaluate your specific environment before installing VFDs. Consult with your product supplier or a qualified engineer about the feasibility of using VFDs in your facility.